

Copper and lead cannot be used in contact with or even above aluminium, zinc, or coated steel without an increased risk of premature corrosion. Metal flashing should be provided with expansion joints on long runs to prevent deformation of the metal sheets due to expansion and contraction, and should not stain or be stained by adjacent materials or react chemically with them.Īn important type of potential chemical reaction between metal flashing materials is galvanic corrosion. Metal flashing materials include lead, aluminium, copper, stainless steel, zinc alloy, other architectural metals or a metal with a coating such as galvanized steel, lead-coated copper, anodized aluminium, terne-coated copper, galvalume (aluminium-zinc alloy coated sheet steel), and metals similar to stone-coated metal roofing. Most flashing materials today are metal, plastic, rubber, or impregnated paper. In earlier days, birch bark was occasionally used as a flashing material. Exposed flashing is usually of a sheet metal and concealed flashing may be metal or a flexible, adhesive backed, material particularly around wall penetrations such as window and door openings. gives instruction on installing lead flashing and 1875 Notes on Building Construction gives detailed instruction and is well illustrated with methods still used today. In builders books, by 1832 Loudons An Encyclopædia of Cottage, Farm, and Villa Architecture and Furniture. Moreover, flashing is important to ensure integrity of the roof prior to a solar panel installation. It is also essential to prevent leaks around skylights or roof windows. thus making buildings more durable and reducing indoor mold problems. The introduction of manufactured flashing decreased water penetration at obstacles such as chimneys, vent pipes, walls which abut roofs, window and door openings, etc. These methods included angling roof shingles away from the joint, placing chimneys at the ridge, building steps into the sides of chimneys to throw off water and covering seams between roofing materials with mortar flaunching. Flashing may be let into a groove in a wall or chimney called a reglet.īefore the availability of sheet products for flashing, builders used creative methods to minimize water penetration. The up-hill side of a chimney may have a small gable-like assembly called a cricket with cricket flashing or on narrow chimneys with no cricket a back flashing or back pan flashing.
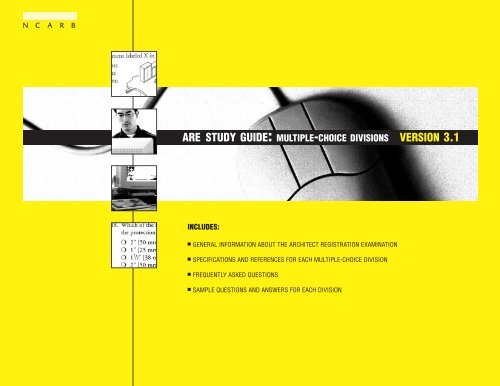
Strips of lead used for flashing an edge were sometimes called an apron, and the term is still used for the piece of flashing below a chimney. Ĭounter-flashing (or cover flashing, cap flashing) is a term used when there are two parallel pieces of flashing employed together such as on a chimney, where the counter-flashing is built into the chimney and overlaps a replaceable piece of base flashing. The origin of the term flash and flashing are uncertain, but may come from the Middle English verb flasshen, 'to sprinkle, splash', related to flask.
